
The Engineers Tool: Punches.

Introduction:
Tool consisting of metal rod with conical point and it is used for making an indentation and to allow a punch make holes at same spot without slipping. There are different types of punches of which some of them are Centre punch, nail punch, pin punch, drill punch and prick punch etc. A punch press is designed specifically for the making of various shaped holes and coutouts on metal sheets and plate. The punches are fitted in punche press, also the dies of the size and ashape of the hole required. For irregular and non standard holes, the modem punch press is capable of nibbling. This refers to a series of successive its following a predetermined pattern that creates the cutout.
The punching action is accomplished by a vertical moving ram that forces the punch through the material and into a die through which the resulting slug is ejected. Additionally, a device to hold the material in place as a punch is withdrawn , calls a stripper , and is often and integral part of the punch tool.
Types of Punches:

Please scroll horizontally for details.
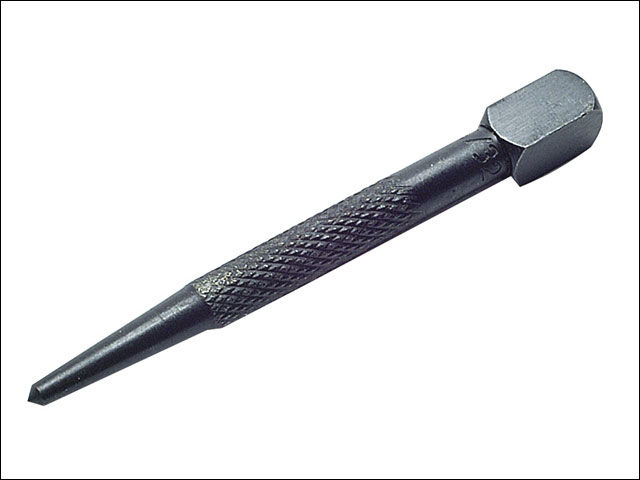
A centre punch is used to mark the center of a point. It is usually used to mark the centre of a hole when drilling holes. A drill has the tendency to "wander" if it does not start in a recess. A centre punch forms a large enough dimple to "guide" the tip of the drill. The tip of a centre punch has an angle between 60 and 90 degrees. When drilling larger holes, and the web of the drill is wider than the indentation produced by a centre punch, the drilling of a pilot hole is usually needed.
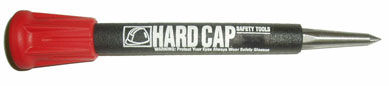
A prick punch is similar to a center punch but used for marking out. It has a sharper angled tip to produce a narrower and deeper point. It is also known as a dot punch. The mark can then be enlarged with a centre punch for drilling. The tip of a prick punch is 40 degrees (the angle depends on what type of prick punch you are using.)

Please scroll horizontally for details.
Punch Selection:
The group was divided and each group had to make specific type of Punches. As per discussion within th group, we have concluded to Centre Punch manufacture. The image has been shown below.

Manufacturing Procedure:
The complete manufacturing can be carried out in a typical Lathe Machine. However, there are certain amount of proesses that includes while manufacturing.
The principle purpose of the engine Lathe is to reduce materials from a required material by revaluing if against a cutting tools. The cutting tools either moves along the work piece (turning) or across the work piece (facing) external or external surface can be used for machined in a lathe. The engine lathe can also be used for drilling, reaming, baring, threading & many specialized operation. Our job is to make a center punch respectively doing various processes such as measuring, facing, turning, knurling etc. with the help of lathe machine. We will also have to define the taper angle.
The brief details are given below.
Tools Required:
1. Lathe Machine
2. Steel Rule
3. Outside Caliper
4. Knurling Tools
5. File
6. Hacksaw
7. Goggles
8. Brush
Processes in Lathe Machine:
1. Chucking
This process is used to assemble the specimen in the Lathe Machine.
2. Countersink / CombinationTurning
These tools allow the specimen to narrow down into dimension.
3. Facing
It is the lathe operation of finishing the ends of the work to make the ends flat & smooth & to make the piece of the required length for this work the job is held in a chuck.
4. Taper Turning
A job which decreases in diameter gradually so that it assumes a conical shape is said to be tapered. Taper angle is the angle, included between the tapering sides of the job when extended to meet at a point.
5. Knurling
It is the process of embowering a diamond shaped regular patterns on the surface of a work piece using a special knurling.
![]() Chucking Works |
---|
![]() facing |
![]() Turning |
![]() tapering |
![]() knurling |
Precauions:
1. Sliding parts of the lathe should be cleaned & lubricated.
2. Speed selector control should not be changed when the spindle is rotating.
3. The carriage clamping screw should be unlocked before moving the carriage.
4. If the chuck is moving forward reverse switch should not be operated.
5. Chips should be changed using a brush.
6. We should use correct size of lathe centers.
7. We should set up correct angle in the lathe machine to get the taper angle.
Tools on Lathe Machine
Out of so many tools that can be applied on the lathe macine to get the desired specimen, only few of the tools will be required in order to make the punches. The tools are as follows:
Facing Turning Tool:
This is used to cut the specimen and narrow down its radius. And at the same time it is used to polish and remove the unwanted materials on the surface.
Taper Turning Tool:
This tool is required to give the sample its conical pointy shape. As it cuts the specimen on a specific angle.
Cut-and-face Milling Tool:
The side-and-face cutter is designed with cutting teeth on its side as well as its circumference. They are made in varying diameters and widths depending on the application. The teeth on the side allow the cutter to makeunbalanced cuts (cutting on one side only) without deflecting the cutter as would happen with a slitting saw or slot cutter
Diamond Knurling Tool:
This tool, as the name mentions, uses to make the knurls on given pitch and spacing at the specimen.
![]() Facing to Polish the material | ![]() Facing Tools |
---|---|
![]() taperturning Tools | ![]() 3-6 |
![]() Milling For Hexagonal Shape | ![]() Diamond Knurling Tools |
Heat Treatment:
Heat treatment is a process which we use to improve the metallurgical properties (physically, chemical and mechanical) and molecular structure of materials and alloys without change in shape as our requirement. It improves the strength and performance of material. Mostly heat treatment is used in glass and metals industries. Heat treatment has following steps.
Hardening
In hardening we heat the object above its critical temperature. We did this step in our laboratory with muffle oven. We heat the punch round about 800C in muffle oven. Hardening is used to improve the hardness of material.
Quenching
When object heated till its critical temperature then immediately put the object in the cool liquid water or oil. Quenching gives the more hardness. It is the part of hardening. We put the punch into the water.
Tempering
In this process we give the low heat to object. After quenching may be it is possible object’s molecules will little bit damage because we change the environment suddenly. This process increase the ductility and toughness of the material. We used gas torch.
![]() Heat-Treating-Furnace | ![]() quenching |
---|---|
![]() Tempering |